Lean Manufacturing Consulting
Transform your manufacturing operations by eliminating waste, optimizing processes, and maximizing value with our specialized lean manufacturing consulting services.
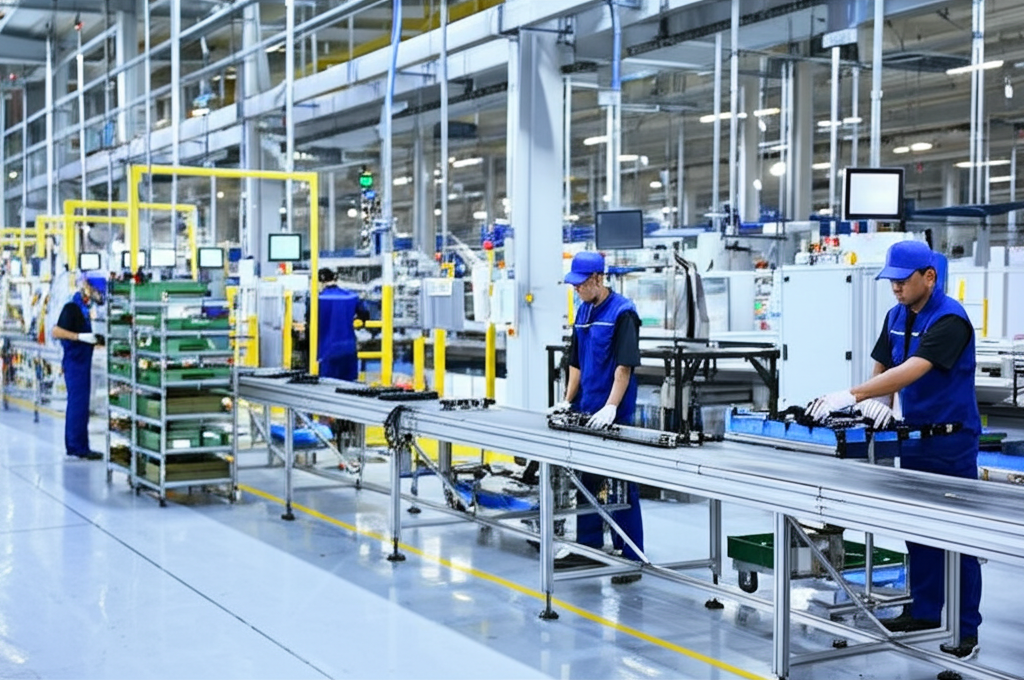
What is Lean Manufacturing?
Lean manufacturing is a methodology that focuses on minimizing waste within manufacturing systems while simultaneously maximizing productivity. It is derived from Toyota's Production System and has been adopted worldwide as a way to improve efficiency, quality, and profitability in manufacturing operations.
At Schapira CPAs, we combine our deep financial expertise with lean manufacturing principles to help manufacturers not only streamline their operations but also translate those operational improvements into measurable financial gains. Our approach goes beyond traditional lean consulting by integrating financial analysis and cost accounting to ensure that lean initiatives deliver maximum ROI.
The 8 Wastes of Manufacturing
Transportation
Unnecessary movement of materials, products or information between processes
Inventory
Excess products and materials that aren't being processed
Motion
Unnecessary movement by people (bending, reaching, walking)
Waiting
Idle time created when material, information, people, or equipment is not ready
Overproduction
Producing more than is needed or before it is needed
Overprocessing
Doing more work than what is required by the customer
Defects
Errors, scrap, rework, and incorrect information
Skills
Underutilizing capabilities and delegating tasks with inadequate training
Benefits of Lean Manufacturing
Reduced Operating Costs
Eliminate waste in processes, inventory, and resources to significantly lower production costs.
Improved Quality
Standardized processes and continuous improvement lead to fewer defects and higher product quality.
Increased Productivity
Streamlined workflows and eliminated bottlenecks allow for more efficient production with the same resources.
Enhanced Customer Satisfaction
Faster delivery times, better quality, and more responsive operations lead to happier customers.
Greater Employee Engagement
Lean principles empower employees to identify and solve problems, increasing job satisfaction and retention.
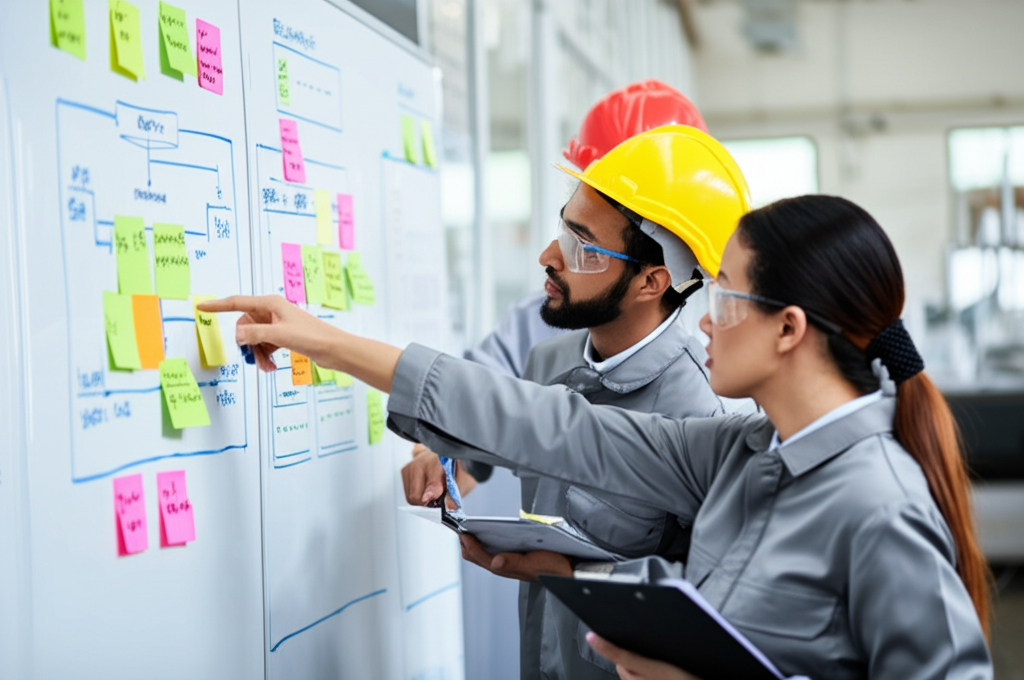
Our Lean Implementation Methodology
Assessment & Value Stream Mapping
We begin by thoroughly analyzing your current operations, identifying value streams, and documenting the current state of your processes. This includes identifying all forms of waste and opportunities for improvement.
Strategic Planning
Based on our assessment, we develop a customized lean implementation plan that aligns with your business goals. We prioritize improvements based on impact, feasibility, and return on investment.
Implementation of Lean Tools
We implement appropriate lean tools and techniques such as 5S, Kanban, SMED, TPM, and cellular manufacturing to address specific areas of waste and inefficiency in your operations.
Employee Training & Engagement
We provide comprehensive training to your team on lean principles and tools, ensuring they have the knowledge and skills to maintain and improve the lean systems we implement.
Continuous Improvement Systems
We establish sustainable continuous improvement processes, including regular kaizen events, performance metrics, and feedback loops to ensure ongoing optimization.
Financial Impact Analysis
We measure and document the financial impact of lean improvements, helping you quantify ROI and identify further opportunities for cost reduction and efficiency gains.
Success Story
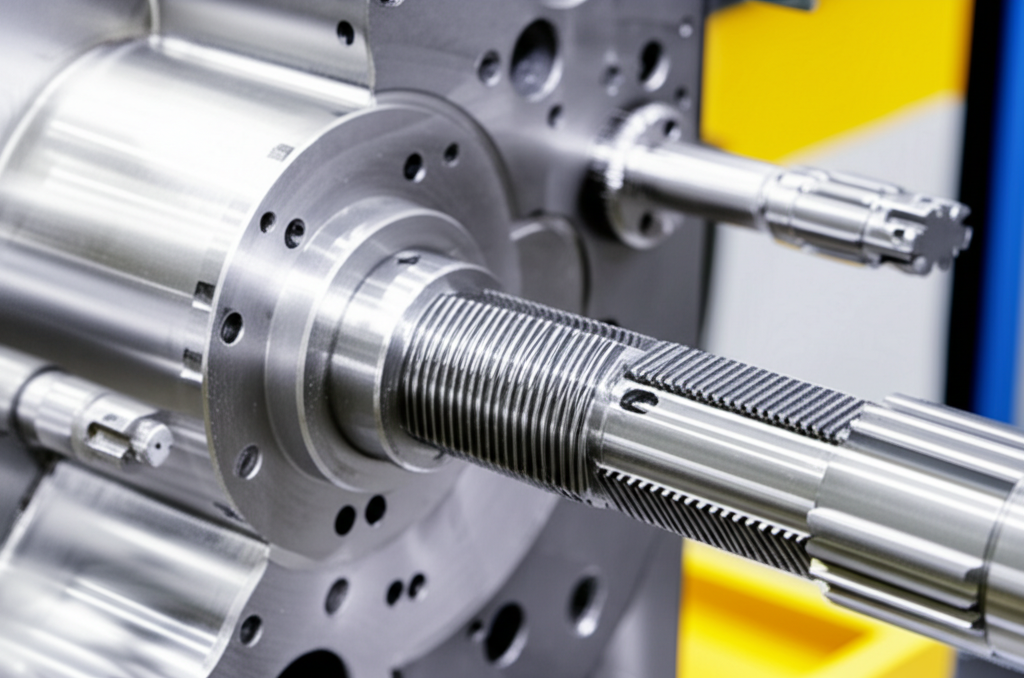
Precision Metal Manufacturer Reduces Lead Time by 62%
A precision metal components manufacturer with 120 employees was struggling with long lead times, high inventory levels, and inconsistent quality. Their customers were demanding faster delivery and their competitors were gaining market share.
Our team implemented a comprehensive lean transformation program that included:
- Value stream mapping to identify bottlenecks and waste
- 5S workplace organization across all production areas
- Setup time reduction (SMED) on critical equipment
- Pull-based production scheduling with kanban
- Total Productive Maintenance (TPM) implementation
Results:
- 62% reduction in manufacturing lead time
- 43% reduction in work-in-process inventory
- 27% improvement in productivity
- Annual savings of $1.2 million
Key Lean Manufacturing Tools
5S Workplace Organization
Sort, Set in order, Shine, Standardize, and Sustain. A methodology for organizing workspaces to improve efficiency and effectiveness.
Kanban Systems
Visual management tool that helps regulate the flow of goods both within the factory and with outside suppliers and customers.
Value Stream Mapping
A lean tool that employs a flowchart to document every step in the process and identify waste and opportunities.
Single-Minute Exchange of Dies (SMED)
A system for dramatically reducing the time it takes to complete equipment changeovers, enabling smaller batch sizes.
Total Productive Maintenance (TPM)
A holistic approach to equipment maintenance that strives to achieve perfect production with no breakdowns.
Cellular Manufacturing
Arranging factory floor equipment in a sequence that supports a smooth flow of materials with minimal transport or delay.
The Schapira CPA Difference
Financial Expertise Integration
We uniquely combine lean operational expertise with deep financial knowledge to ensure improvements translate to bottom-line results.
Industry-Specific Knowledge
Our consultants have specialized experience in manufacturing sectors including aerospace, automotive, medical devices, and consumer goods.
Practical Implementation Focus
We don't just provide recommendationsβwe work alongside your team to implement changes and ensure sustainable results.
ROI-Driven Approach
Every improvement we recommend is evaluated based on its financial impact and return on investment.
Comprehensive Support
From initial assessment through implementation and continuous improvement, we provide end-to-end support for your lean journey.
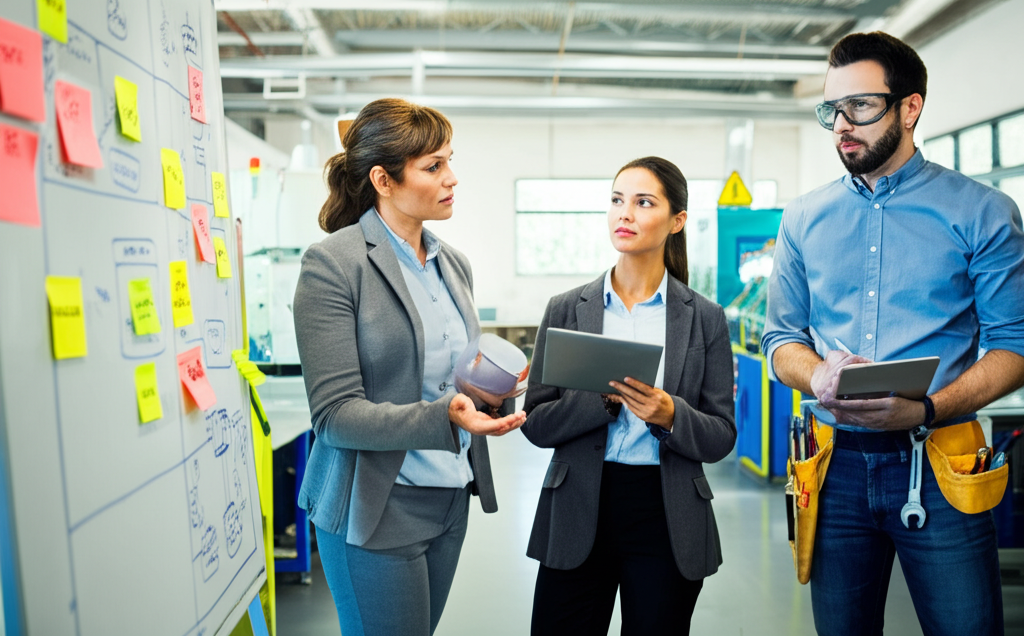
Frequently Asked Questions
How long does it typically take to implement lean manufacturing?
The timeline varies based on the size of your operation and the scope of implementation. Initial improvements can often be seen within 3-6 months, while a full lean transformation may take 1-2 years. We focus on quick wins early in the process to generate momentum and ROI.
Is lean manufacturing only for large manufacturers?
No, lean principles can be applied to manufacturing operations of any size. In fact, smaller manufacturers often see results more quickly due to their agility and ability to implement changes rapidly. We tailor our approach to fit the specific needs and scale of your business.
How do you ensure lean improvements are sustained over time?
Sustainability is built into our methodology. We focus on cultural change, employee engagement, establishing measurement systems, and creating standardized processes. We also provide ongoing support and check-ins to ensure improvements are maintained and continuous improvement becomes part of your company culture.
What kind of ROI can we expect from lean manufacturing implementation?
While results vary by company, our clients typically see a 3:1 to 5:1 return on their investment in lean consulting services. Common areas of financial impact include reduced inventory carrying costs, lower scrap rates, improved labor productivity, reduced space requirements, and increased capacity.
How does lean manufacturing relate to other improvement methodologies like Six Sigma?
Lean manufacturing focuses primarily on eliminating waste and improving flow, while Six Sigma focuses on reducing variation and improving quality. Many companies adopt a Lean Six Sigma approach that combines both methodologies. We can help you determine the right approach for your specific challenges and goals.
Ready to Transform Your Manufacturing Operations?
Contact us today to schedule a no-obligation consultation and discover how our lean manufacturing consulting services can help you reduce waste, improve efficiency, and boost your bottom line.
Related Services
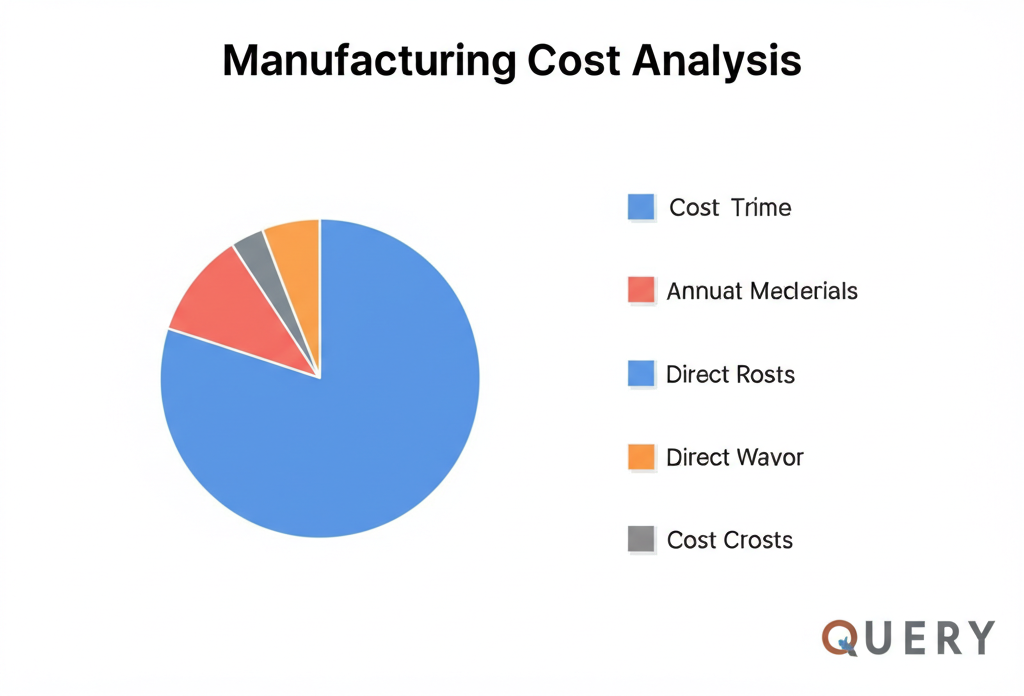
Cost Accounting Analysis
Gain visibility into your true product costs and identify opportunities for improvement.
Learn more β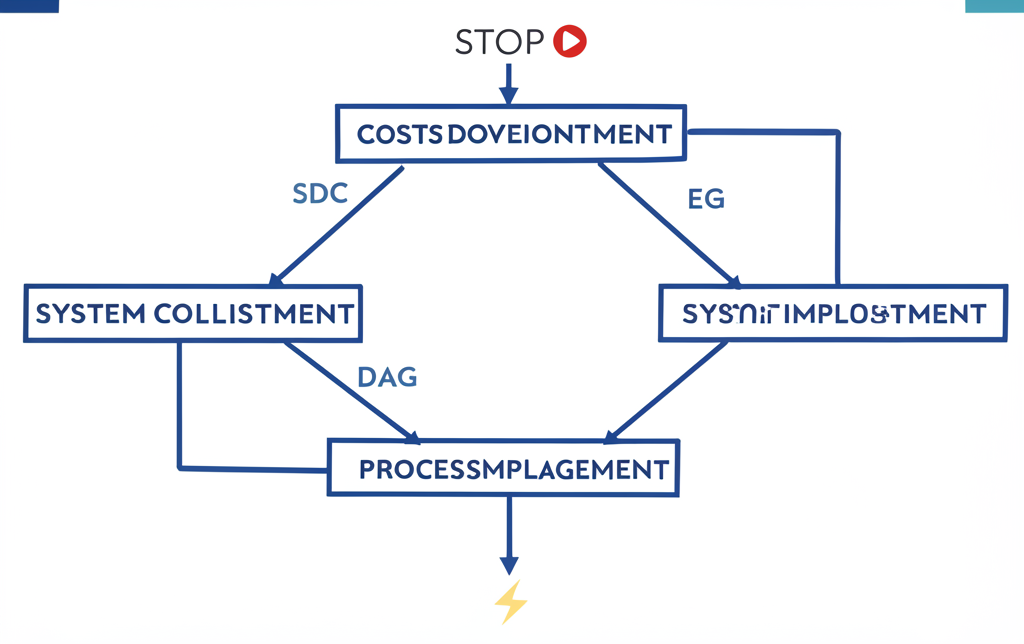
Cost Accounting Implementation
Implement effective cost accounting systems tailored to your manufacturing processes.
Learn more β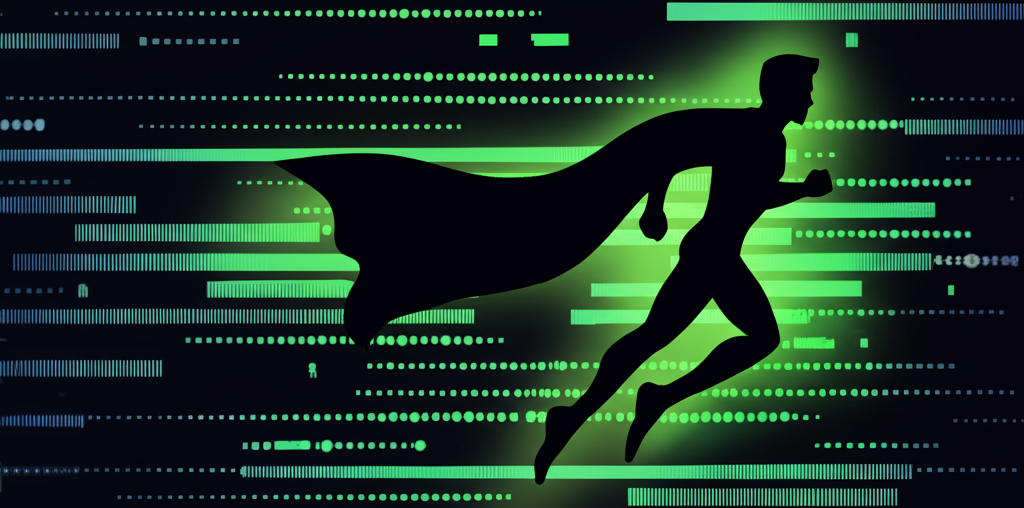
Cost Optimization
Strategic approaches to reduce and control manufacturing costs.
Learn more β