In today's competitive manufacturing environment, understanding your true costs is essential for making informed decisions, optimizing operations, and maintaining profitability. Schapira CPA's Manufacturing Cost Analysis service provides a comprehensive examination of your production costs, identifying inefficiencies, uncovering hidden expenses, and revealing opportunities for strategic improvements.
The Power of Detailed Cost Analysis
Our manufacturing cost analysis goes beyond standard financial reporting to provide actionable insights into the true economics of your production processes. We examine every aspect of your manufacturing costs, including:
- Direct Material Costs: Analysis of material usage, waste, scrap rates, supplier pricing, and inventory management.
- Direct Labor Costs: Evaluation of labor efficiency, productivity metrics, overtime patterns, and labor allocation across production lines.
- Manufacturing Overhead: Detailed breakdown of fixed and variable overhead costs, including utilities, maintenance, depreciation, and indirect labor.
- Product-Level Profitability: Accurate cost allocation to determine true profitability by product line, customer, or market segment.
- Cost Variances: Identification of variances between standard and actual costs, with root-cause analysis.
Our Cost Analysis Methodology
1. Data Collection & Assessment
We begin by gathering comprehensive cost data from your ERP system, production records, financial statements, and operational metrics. Our team works closely with your production, finance, and engineering departments to ensure we have a complete picture.
2. Cost Structure Mapping
We create detailed cost structure maps for each product line and production process, identifying all direct and indirect costs. This visualization helps identify cost drivers and relationships between different cost elements.
3. Activity-Based Analysis
Using activity-based costing principles, we allocate costs based on actual resource consumption rather than arbitrary allocations. This provides a more accurate picture of true product costs and profitability.
4. Variance Analysis
We analyze variances between standard and actual costs, identifying patterns and root causes. This helps distinguish between one-time anomalies and systemic issues requiring attention.
5. Benchmarking
We compare your cost structure against industry benchmarks and best practices to identify areas where your costs may be out of line with industry standards or where there are opportunities for improvement.
6. Actionable Recommendations
Based on our analysis, we provide specific, actionable recommendations for cost optimization, prioritized by potential impact and implementation difficulty.
Key Benefits for Manufacturers
Improved Profitability
Identify underperforming products, unprofitable customers, and opportunities to optimize pricing strategies based on true costs.
Strategic Decision Support
Make informed decisions about product mix, make-vs-buy decisions, capital investments, and production planning based on accurate cost data.
Operational Efficiency
Identify inefficiencies in production processes, excessive waste, and opportunities to streamline operations and reduce costs.
Common Cost Analysis Challenges We Solve
Inaccurate Product Costing
Many manufacturers rely on outdated or oversimplified costing methods that fail to capture the true cost of producing each product. This can lead to mispriced products, unprofitable orders, and misguided strategic decisions.
Our Solution: Implementation of activity-based costing methodologies that accurately reflect resource consumption and provide true product-level profitability insights.
Hidden Cost Drivers
Manufacturers often struggle to identify the underlying drivers of cost increases or variances, particularly in complex production environments with multiple product lines.
Our Solution: Detailed cost driver analysis that identifies the root causes of cost variances and provides actionable insights for addressing them.
Ineffective Overhead Allocation
Traditional overhead allocation methods often distribute costs based on direct labor hours or machine hours, which may not reflect the actual consumption of overhead resources by different products.
Our Solution: Development of more sophisticated overhead allocation methodologies that better reflect the causal relationships between products and overhead costs.
Lack of Cost Visibility
Many manufacturers lack visibility into costs at a granular level, making it difficult to identify specific areas for improvement or to understand the cost implications of different decisions.
Our Solution: Implementation of cost transparency frameworks and reporting tools that provide clear visibility into costs at multiple levels of detail.
Real Results: Cost Analysis in Action
Case Study: Precision Components Manufacturer
A precision components manufacturer with $12M in annual revenue was experiencing declining margins despite stable sales. Their existing costing system allocated overhead based on direct labor hours, which had become increasingly irrelevant as automation increased.
Our Approach:
- Conducted a comprehensive cost structure analysis
- Implemented activity-based costing for overhead allocation
- Developed product-level profitability analysis
- Created a new cost reporting framework
Results:
The analysis revealed that 15% of products were significantly unprofitable. By adjusting pricing on some products and discontinuing others, the company improved gross margins by 4.2 percentage points, resulting in $504,000 in additional annual profit.
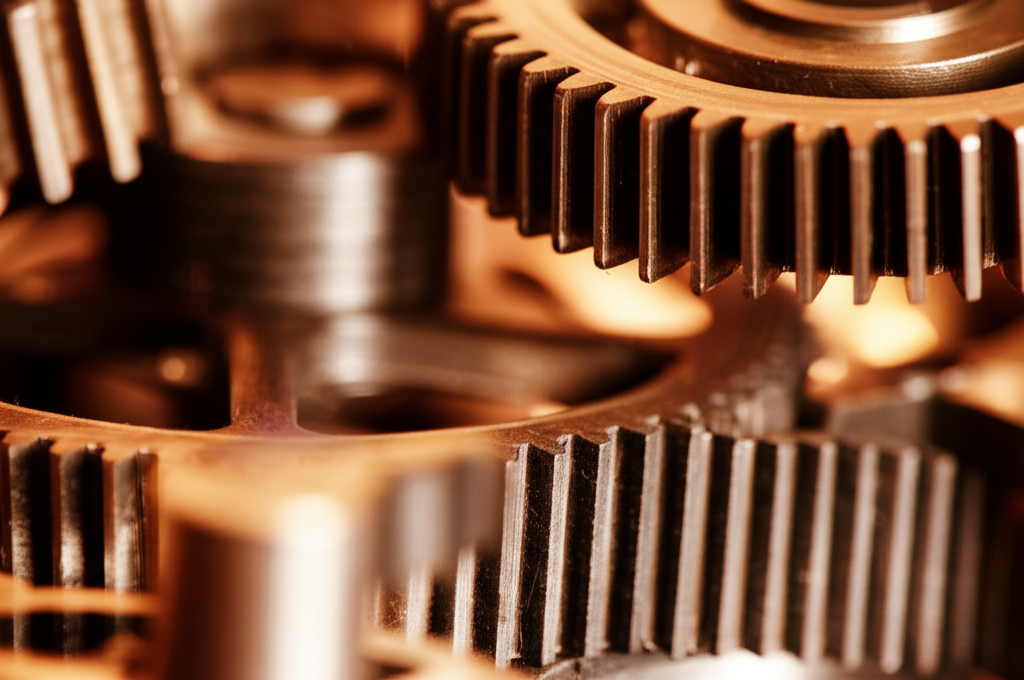
Transform Your Manufacturing Cost Management
Ready to gain deeper insights into your manufacturing costs? Contact Schapira CPA today to discuss how our Cost Analysis services can help you identify inefficiencies, optimize operations, and improve profitability.
Request a Cost Analysis Consultation