In today's competitive manufacturing landscape, optimizing costs is not just about cutting expenses—it's about strategically allocating resources to maximize value and maintain quality. Schapira CPA's Manufacturing Cost Optimization service helps you identify, reduce, and control costs across your operations while preserving product quality and supporting growth objectives.
Strategic Cost Optimization vs. Simple Cost Cutting
There's a critical difference between strategic cost optimization and indiscriminate cost cutting. While cost cutting often focuses on short-term expense reduction that can compromise quality and capacity, strategic cost optimization takes a holistic approach that:
- Aligns with Business Strategy: Ensures cost initiatives support your long-term business objectives and competitive positioning.
- Preserves Value Creation: Maintains or enhances the value delivered to customers while eliminating waste and inefficiency.
- Focuses on Total Cost of Ownership: Considers the full lifecycle cost impact of decisions rather than just immediate savings.
- Builds Sustainable Advantage: Creates structural cost advantages that competitors cannot easily replicate.
- Enables Investment in Growth: Frees up resources that can be redirected to innovation and market expansion.
Our Cost Optimization Methodology
Comprehensive Cost Assessment
We begin with a thorough analysis of your current cost structure, identifying all direct and indirect costs across your manufacturing operations. This includes detailed examination of materials, labor, overhead, and supply chain costs.
Benchmarking & Gap Analysis
We compare your cost structure against industry benchmarks and best practices to identify areas where your costs may be out of line with industry standards. This helps prioritize optimization efforts where they'll have the greatest impact.
Opportunity Identification
Based on the assessment and benchmarking, we identify specific cost optimization opportunities across your operations. Each opportunity is evaluated for potential savings, implementation complexity, and impact on operations.
Strategy Development
We develop detailed strategies for each optimization opportunity, including implementation plans, resource requirements, timeline, and expected ROI. These strategies are prioritized based on impact, feasibility, and alignment with your business objectives.
Implementation Support
We provide hands-on support during the implementation phase, working closely with your team to execute the optimization strategies. This includes process redesign, system configuration, vendor negotiations, and change management.
Monitoring & Continuous Improvement
We establish metrics and monitoring systems to track the results of optimization initiatives and identify opportunities for further improvement. This creates a culture of continuous cost optimization rather than one-time cost cutting.
Key Cost Optimization Areas for Manufacturers
Material Cost Optimization
- Strategic sourcing and vendor management
- Material yield improvement
- Scrap and waste reduction
- Inventory optimization
- Make vs. buy analysis
Labor Productivity Enhancement
- Workforce planning and scheduling
- Skills development and cross-training
- Process standardization
- Automation of repetitive tasks
- Incentive program design
Overhead Cost Reduction
- Energy efficiency improvements
- Maintenance optimization
- Facility space utilization
- Administrative process streamlining
- Shared service implementation
Supply Chain Optimization
- Logistics network design
- Transportation mode optimization
- Warehouse efficiency improvement
- Supplier consolidation
- Just-in-time implementation
Quality Cost Management
- Defect prevention strategies
- Inspection optimization
- Warranty cost reduction
- Process capability improvement
- Root cause analysis systems
Product Cost Engineering
- Design for manufacturability
- Value engineering
- Component standardization
- Product portfolio rationalization
- Target costing implementation
The Schapira CPA Difference in Cost Optimization
Manufacturing-Specific Expertise
Our team brings deep manufacturing industry knowledge that allows us to identify cost optimization opportunities specific to your production environment. We understand the unique cost drivers and operational constraints of manufacturing businesses.
Data-Driven Approach
We leverage advanced data analytics to identify cost patterns, anomalies, and opportunities that might not be visible through traditional analysis. This ensures that optimization efforts are targeted where they'll have the greatest impact.
Cross-Functional Perspective
Our approach considers the interconnections between different functional areas, ensuring that cost optimization in one area doesn't create unintended consequences in another. We take a holistic view of your operations.
Implementation Focus
We don't just identify opportunities and make recommendations—we work alongside your team to implement changes and ensure they deliver the expected results. Our hands-on approach ensures that savings materialize.
Cost Optimization Success Story
Case Study: Precision Metal Components Manufacturer
A precision metal components manufacturer with $18M in annual revenue was facing margin pressure due to rising material costs and increasing competition. Despite previous cost-cutting efforts, they were struggling to maintain profitability without compromising quality.
Our Approach:
- Conducted comprehensive cost structure analysis across all operations
- Identified material yield improvement opportunities through process modifications
- Implemented strategic sourcing for key raw materials
- Redesigned production scheduling to reduce overtime and setup times
- Optimized inventory levels to reduce carrying costs while maintaining service levels
Results:
Within 12 months, the company achieved a 7.2% reduction in total manufacturing costs, representing approximately $650,000 in annual savings. Material yield improved by 4.3%, overtime was reduced by 62%, and inventory carrying costs decreased by 28%. Most importantly, these improvements were achieved without compromising product quality or delivery performance.
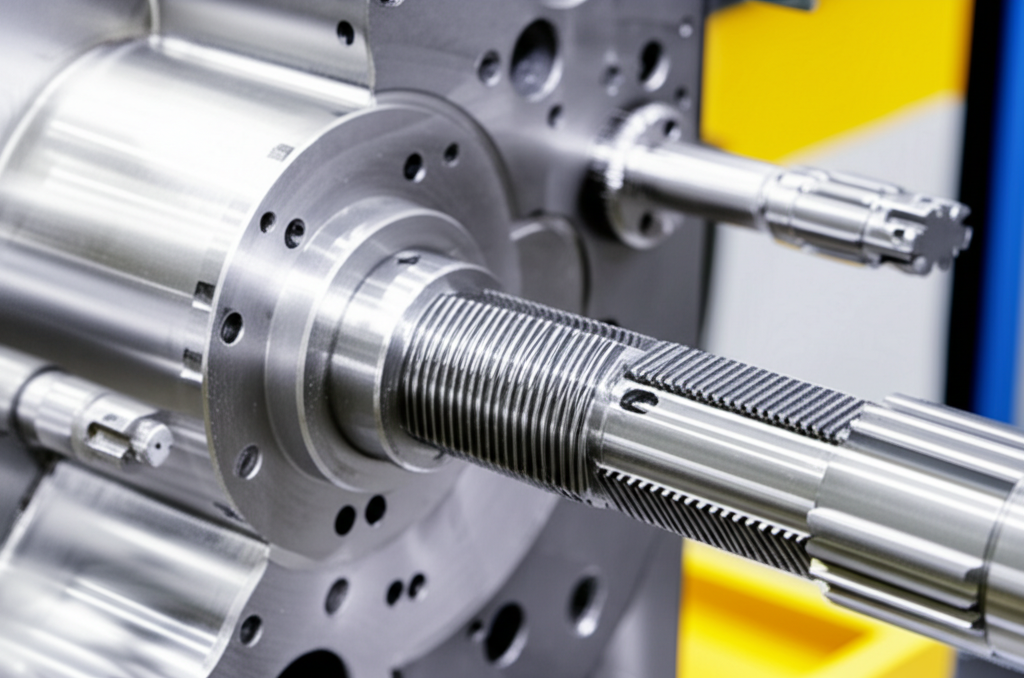
Common Cost Optimization Myths
Let's address some misconceptions about manufacturing cost optimization
Myth: Cost Optimization Means Cutting Jobs
Reality: Effective cost optimization often focuses on eliminating waste and inefficiency, not people. In many cases, optimization actually creates capacity for growth and can lead to job creation rather than reduction.
Myth: Lower Cost Always Means Lower Quality
Reality: Strategic cost optimization targets waste and inefficiency, not value. In fact, many quality improvement initiatives also reduce costs by eliminating defects, rework, and warranty claims.
Myth: Cost Optimization is a One-Time Project
Reality: Sustainable cost optimization is an ongoing process and mindset, not a one-time event. The most successful manufacturers embed cost consciousness into their culture and continuously seek improvement.
Myth: We've Already Cut All Possible Costs
Reality: Even the most efficient manufacturers have optimization opportunities. New technologies, changing market conditions, and evolving best practices create ongoing opportunities for improvement.
Optimize Your Manufacturing Costs
Ready to strategically reduce and control your manufacturing costs while maintaining quality and supporting growth? Contact Schapira CPA today to discuss how our Cost Optimization services can improve your profitability.
Request a Cost Optimization Assessment