For manufacturing businesses, an effective cost accounting system is not just a financial tool—it's a strategic asset that drives profitability and competitiveness. Schapira CPA specializes in implementing tailored cost accounting systems that provide accurate visibility into production costs, support informed decision-making, and create a foundation for continuous improvement.
Why Implement a Specialized Cost Accounting System?
Generic accounting systems often fall short in manufacturing environments, where complex production processes, multiple cost drivers, and varied product lines require specialized approaches to cost tracking and allocation. A properly implemented cost accounting system delivers:
- Accurate Product Costing: Understand the true cost of each product, including direct materials, direct labor, and properly allocated overhead.
- Informed Pricing Decisions: Set competitive yet profitable prices based on actual costs rather than estimates or industry averages.
- Production Efficiency Insights: Identify inefficiencies, waste, and opportunities for process improvement through detailed cost tracking.
- Enhanced Budgeting and Forecasting: Create more accurate budgets and forecasts based on reliable historical cost data.
- Strategic Decision Support: Make informed decisions about product mix, make-vs-buy choices, capital investments, and capacity planning.
Our Implementation Approach
Implementing an effective cost accounting system requires more than just software—it demands a thoughtful approach that aligns with your manufacturing processes, organizational structure, and strategic objectives. Our comprehensive implementation methodology includes:
1. Assessment & Planning
We begin by thoroughly understanding your manufacturing processes, current accounting practices, and strategic objectives. This includes evaluating your existing systems, identifying key stakeholders, and defining clear implementation goals and success metrics.
2. System Design
Based on our assessment, we design a cost accounting system tailored to your specific needs. This includes defining cost centers, cost objects, allocation methodologies, and reporting requirements. We also evaluate and recommend appropriate software solutions when needed.
3. Process Development
We develop detailed processes for cost data collection, validation, allocation, and reporting. This includes creating standard operating procedures, data flow diagrams, and control mechanisms to ensure data integrity and system reliability.
4. Implementation & Integration
We implement the designed system, which may include configuring software, developing custom reports, integrating with existing systems (ERP, MRP, etc.), and establishing data flows. We ensure seamless integration with your production and financial systems.
5. Training & Change Management
We provide comprehensive training for all system users, from shop floor personnel to financial analysts and executives. Our change management approach ensures smooth adoption and minimizes disruption to your operations.
6. Validation & Optimization
After implementation, we validate the system's accuracy and effectiveness, making necessary adjustments to ensure it delivers the expected benefits. We also establish processes for continuous improvement and system evolution as your business grows and changes.
Key Components of an Effective Manufacturing Cost System
Bill of Materials Management
Accurate tracking of material costs through detailed bills of materials that reflect current costs, waste factors, and engineering changes.
Labor Tracking Systems
Efficient methods for capturing direct and indirect labor costs, including time tracking, labor routing, and productivity analysis.
Overhead Allocation
Sophisticated allocation methodologies that accurately distribute overhead costs based on appropriate cost drivers and activity-based principles.
Variance Analysis
Systematic comparison of standard and actual costs to identify and address inefficiencies, with root-cause analysis capabilities.
Integration Capabilities
Seamless integration with ERP, MRP, production control, and financial systems to ensure data consistency and eliminate duplicate entry.
Reporting & Analytics
Comprehensive reporting tools that provide actionable insights at various levels, from detailed operational metrics to executive dashboards.
Common Implementation Challenges We Solve
Data Collection Challenges
Many manufacturers struggle with collecting accurate and timely cost data, particularly in high-volume or complex production environments.
Our Solution: We implement streamlined data collection processes that balance accuracy with practicality, often leveraging automation, barcode scanning, or integration with production equipment.
System Integration Issues
Disconnected systems lead to data silos, duplicate entry, and inconsistent information across the organization.
Our Solution: We design integration architectures that connect cost accounting with ERP, MRP, shop floor control, and financial systems, ensuring a single source of truth for cost data.
User Adoption Resistance
New systems often face resistance from users accustomed to existing processes or concerned about increased workload.
Our Solution: Our change management approach emphasizes user involvement in the design process, clear communication of benefits, comprehensive training, and ongoing support to ensure successful adoption.
Complexity vs. Usability Balance
Cost accounting systems must balance the need for detailed accuracy with practical usability for daily operations.
Our Solution: We design systems with appropriate levels of detail for different users and purposes, using automation and intuitive interfaces to manage complexity without sacrificing accuracy.
Implementation Success Story
Case Study: Advanced Electronics Manufacturer
An electronics manufacturer with $25M in annual revenue was struggling with inaccurate product costing that led to pricing issues and eroding margins. Their existing system relied on simplistic allocation methods that didn't reflect the complexity of their multi-stage production process.
Our Approach:
- Implemented a work-cell based cost accounting structure
- Developed activity-based costing for complex overhead allocation
- Integrated with existing ERP system for seamless data flow
- Created custom dashboards for production managers and executives
- Provided comprehensive training for all system users
Results:
Within six months of implementation, the company identified several underpriced products and adjusted pricing strategies. They also discovered inefficiencies in certain production processes that were addressed through targeted improvements. The combined impact increased overall gross margin by 3.2 percentage points, representing approximately $800,000 in additional annual profit.
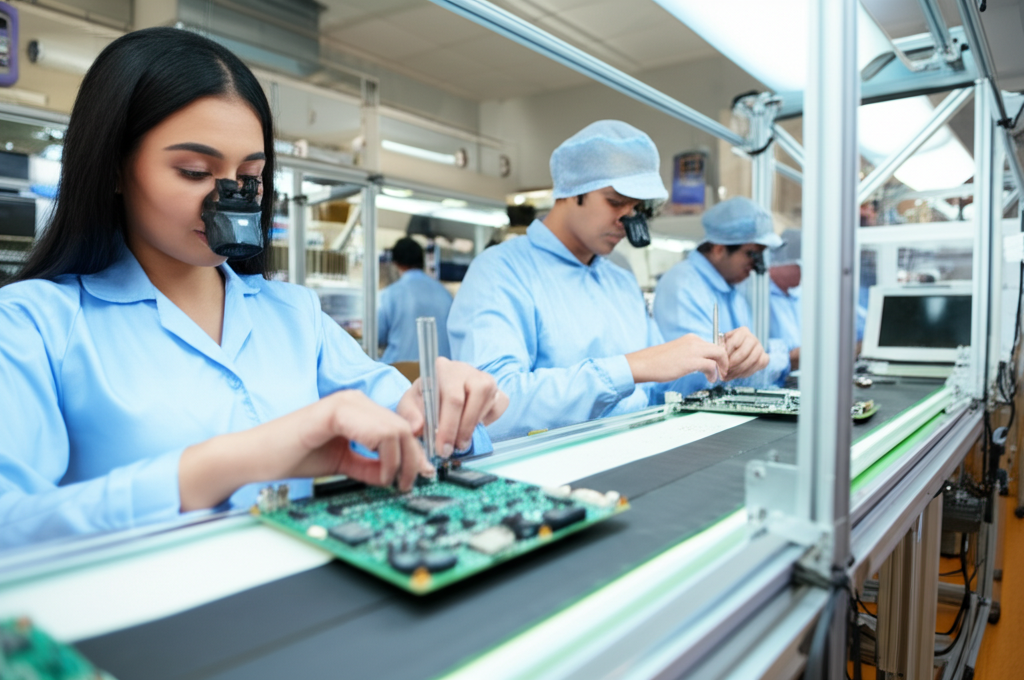
Transform Your Cost Management Capabilities
Ready to implement a cost accounting system that delivers accurate insights and drives profitability? Contact Schapira CPA today to discuss how our implementation services can transform your manufacturing cost management.
Request an Implementation Consultation